6 Reasons Why Quality Control Inspections Must Be Carried Out at All Costs
10 Nov, 202210 minsThe absence of quality control would be inevitable if a factory managed quality and all work...
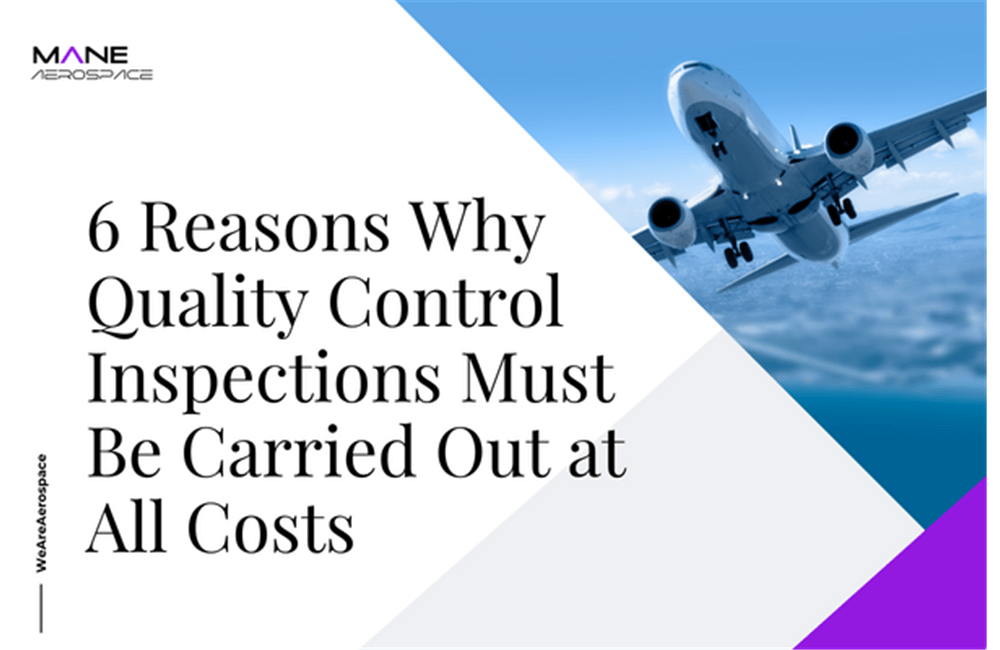
The absence of quality control would be inevitable if a factory managed quality and all workers were responsible for the product outcome. There are, of course, some flaws in this world. There is no such thing as perfect people, so quality control is mandatory even in nations that are highly regarded in the aerospace manufacturing industry.
Substandard rules and regulations in countries that aren’t as developed as the western world make quality much more uncertain. Importers should consider inspections a vital component of supply chain management as a result.
Below, we’ve highlighted the 6 most important reasons why quality controls need to be included in all supply chain planning:
Ensures minimal risk
It is important to consider the risks and dangers associated with sourcing goods from Asia or even smaller suppliers. For instance, taking the short route in production, using inferior materials, seeking substandard production facilities, manufacturing samples that are not identical to sample production, and producing defective goods are all examples. In order to improve the quality of your product, you need quality control inspections.
Power in negotiations
There are cases when a buyer and supplier negotiate the terms of resolution when the supplier's defect level exceeds the acceptable level. Rework and piece-by-piece inspections are sometimes required, while the shipping price may be reduced. As a result of quality control inspections, you will have a much better understanding of the quality status of the products before shipment, allowing you to resolve the situation before additional expenditures are incurred.
Keeping your brand safe
The provision of good quality products contributes to increasing customer satisfaction, loyalty, and trust. A satisfied customer is not only a repeat customer, but can also act as an evangelist for your brand. Your products must meet, or exceed, the expectations of your customers in order to maintain this position. Businesses have been ruined by not remembering this point. As a business, especially in aerospace, maintaining and enhancing the value of your brand and products always depends on the quality of your products.
Cost reductions
Many people aren’t settled with the idea of paying for QC inspections. Any company that has had to deal with product recalls, scrapping of goods, receiving returns, or losing business has come to realise the value of inspections. Experiencing these issues can lead to higher costs, both emotionally and physically, in comparison to spending money on inspections.
Control over suppliers
The presence of quality and factory inspectors will give you more power over your suppliers. Whenever factory owners and workers know that inspections could happen at any point in time, they are more conscientious. As a result, fraudulent activity, poor quality, and inadequate work is less likely to occur. An enhanced level of control over the whole manufacturing process is one of the most important benefits, as well as the ability for intervention whenever needed and to do this early on to prevent wasting both money and time also.
Time-saving
There is no doubt that time is one of the most valuable resources in any business. The loss of time equals the loss of money and the loss of an opportunity. The issues that were mentioned in the preceding section are often highly complex and will require an inordinate amount of time for a solution to be developed. In addition to this, travelling abroad in order to resolve issues with suppliers is a laborious and time-consuming process, so heading them off early is vital. As a result of quality control inspections.